Rolls of core material at Titleist’s Ball Plant III.
Modern golf balls are all “solid core” balls, meaning there is a large rubber core inside the ball. Solid core golf balls became popular starting in 2000 with the introduction and immediate popularity of the original Titleist Pro V1. It was not the first solid core ball, but at that time, most elite golfers were still using “wound balls,” which featured cores made of long pieces of rubber that were tightly wound together to create an energetic, bouncy sphere.
“The core is made mostly from polybutadiene, a synthetic polymer rubber material,” said Titleist’s Derek Ladd, the company’s senior project manager of research and intellectual property. “Polybutadiene is resilient, meaning that it recovers quickly when a stress is applied to it [such as an impact with a golf club]. The more resilient the golf ball core, the higher the energy return [ball speed] when a force is applied to it.”
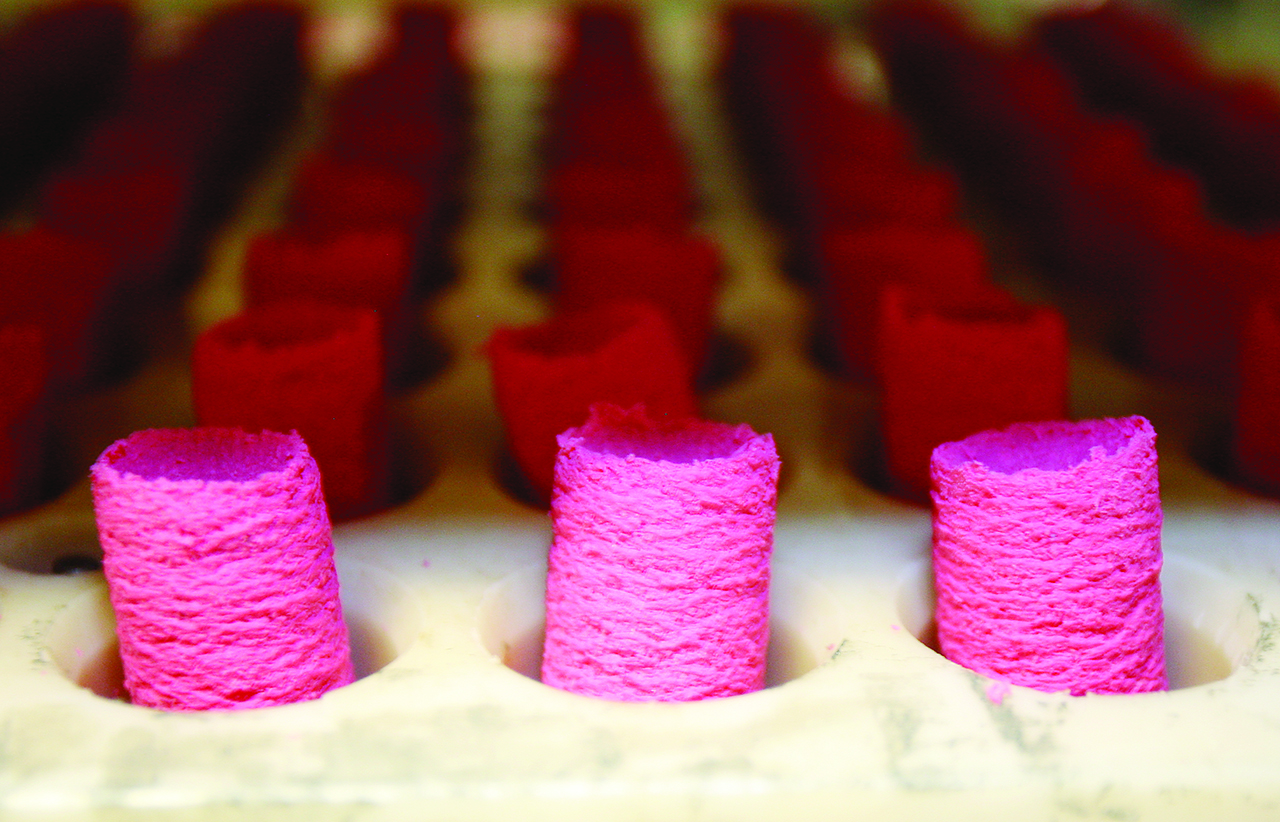
Core molds for the balls at the Titleist Ball Plant III in Fairhaven, Massachusetts. (Golfweek/Tracy Wilcox)
The precise manufacturing techniques that brands use to make balls involve many proprietary machines and methods, but the rubber cores start off as a mixture that resembles cake batter. It is cut into small pieces that look like D-size batteries and placed in molds that are heated and put under high pressure. The process makes the cores perfectly round and much firmer, but they are still bouncy.
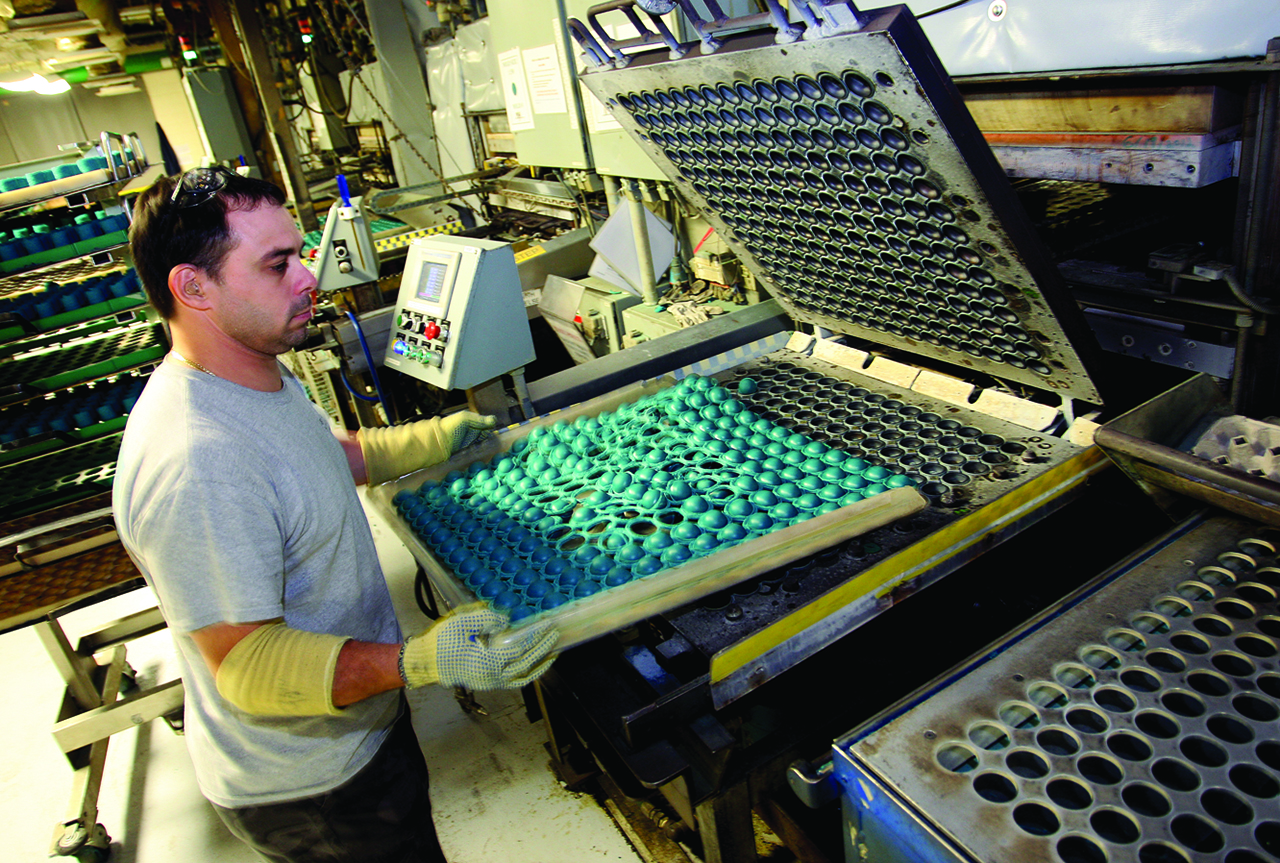
Joel Botelho works in the core molding area at Titleist Ball Plant III in Fairhaven, Massachusetts. (Golfweek/Tracy Wilcox)
Two-piece balls are then given a cover that is usually made from Surlyn or another ionomer. These polymer materials have resins and other stabilizers in them that are also used in the dental industry and as sealants.
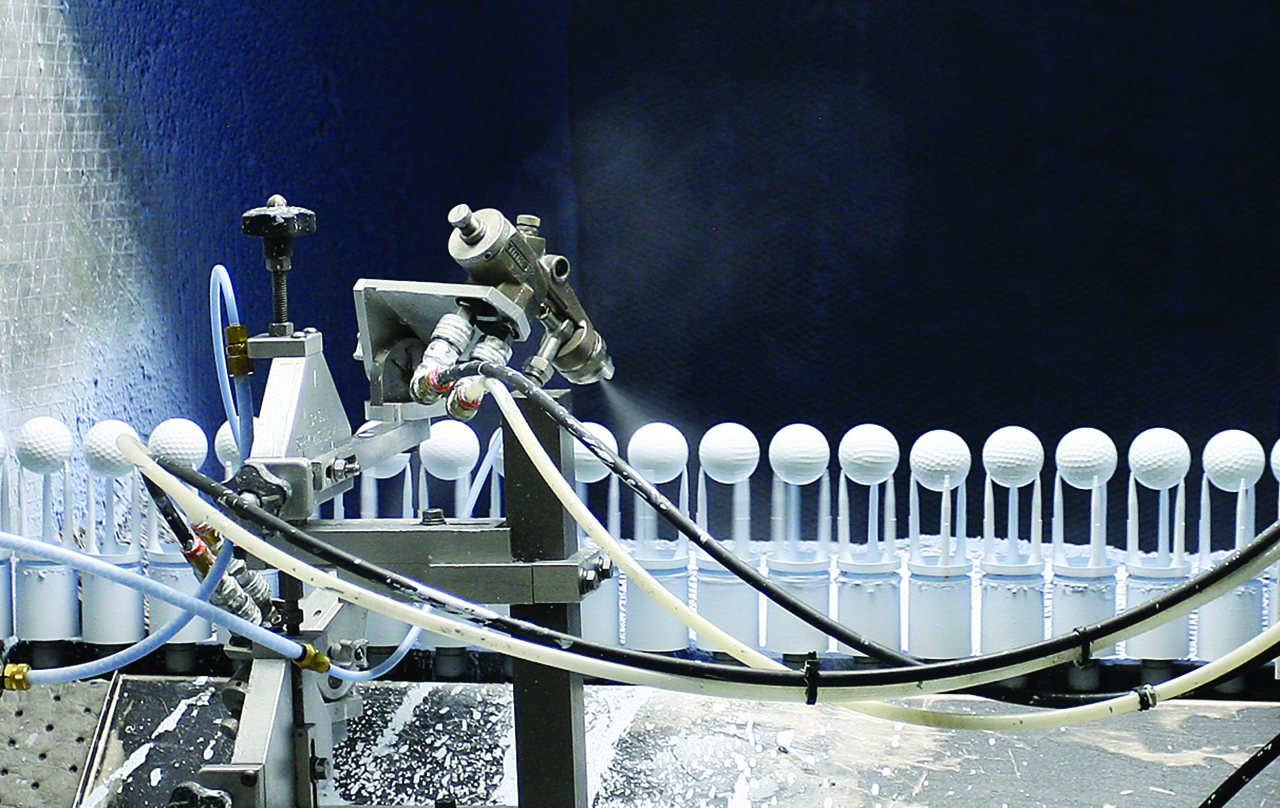
Titleist balls going through the paint process at the Titleist Ball Plant III. (Golfweek/Tracy Wilcox)
After the cover is added, the balls are painted, the numbers and logos are applied, and then a clear-coat material is sprayed over the ball to keep it from getting stained and to help keep the graphics in place.
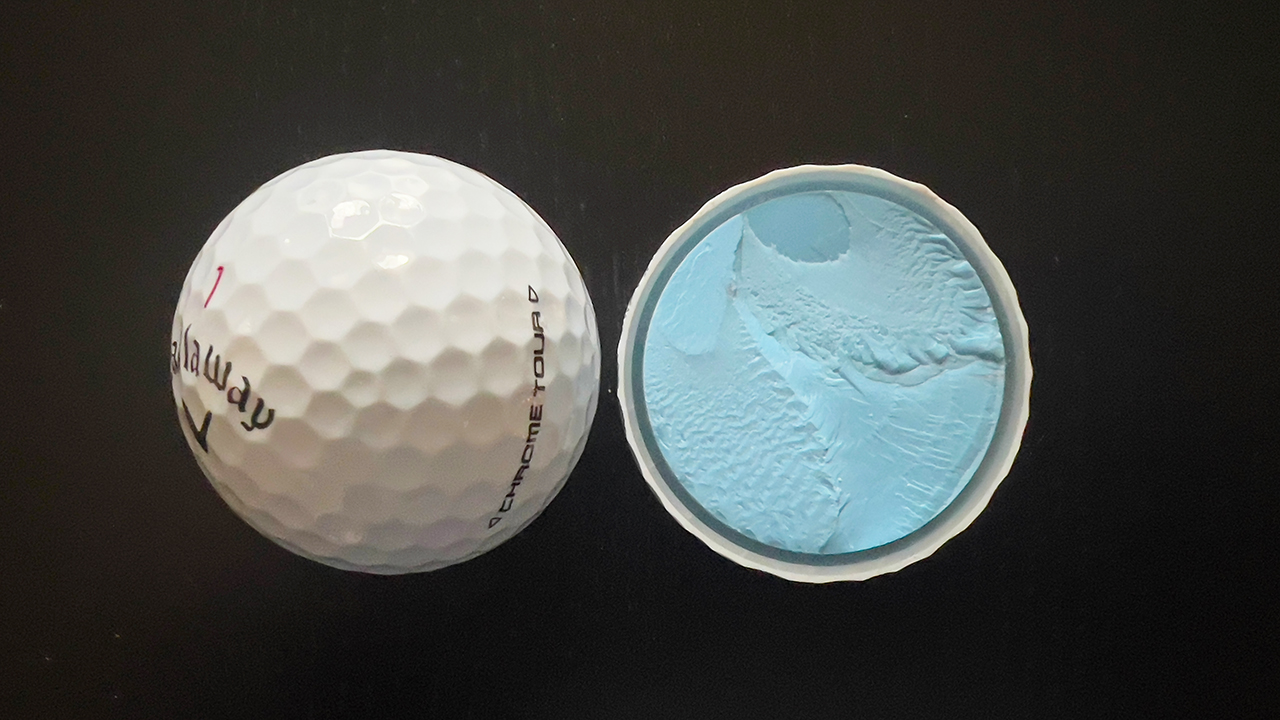
The four-piece 2024 Callaway Chrome Tour has one core and two mantle layers. (David Dusek/Golfweek)
If a manufacturer is making a three-piece golf ball, a casing layer (which is also referred to as a mantle) is added over the core before an ionomer or urethane cover is put on the ball. Four-piece balls may have a dual-core construction, with a small core…
..
Click Here to Read the Full Original Article at Golfweek…